Shopfloor Management reloaded
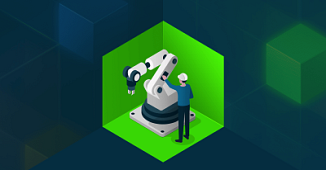
An "old virtue", its stumbling blocks, its potentials - A plea for Tough Skills
Companies in the manufacturing sector regularly suffer internal failure costs that average 1.4 percent of their annual sales, according to the authors of the study. Based on a sales figure of 41 million euros for a typical mechanical engineering company, that would amount to 50,000 euros per month. This poses an enormous challenge – especially for SMEs because small and medium-sized enterprises in particular have only limited human resources and budgets in quality assurance.
At the same time, they often lack suitable software and methods to support the recording, analysis, and elimination of defects that occur throughout the entire value chain. As a result, defects are recorded only inconsistently and incompletely, which leads to considerable additional work in analyzing the error data. Relevant defects are not sufficiently documented and therefore ultimately not resolved.
The solution lies in digitalization. Defect information could be recorded quickly and completely digitally through the targeted use of hardware and software solutions, and passed on to internal databases and systems through the connectivity created.
Dashboards clearly display the defect data recorded and enable defect analysis, which leads to actual defect reduction in manufacturing and process flows. This could significantly reduce the losses, which are estimated at 1.4 percent – provided that the appropriate conditions are created. The authors mention, for example: Easy handling through mobile devices, the use of predefined QR codes, automatic synchronization with the central defect database, stored workflows based on reference processes of defect management – these are all features offered by today's hardware and software solutions.