The Smart Factory Glossary | Part 3
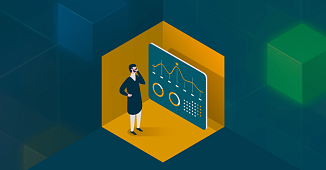
The Smart Factory Glossary | Part 3 – The key acronyms and their definitions
Why is this important? It is important because visions of the future do not describe reality. By their very nature, they are far removed from practice. This remoteness from reality is where their charm – and their danger – lie. Let's focus on one danger here.
Namely, the danger that important and completely realistic steps are not taken because they are too closely intertwined with a goal that does not seem worthwhile. Perhaps the goal is too far in the future, is considered unrealistic – or quite simply it is not a goal that is shared.
It is worth making a distinction here: The smart factory as a field of research refers to the vision of a manufacturing environment in which machines, production facilities, and logistics systems organize themselves without human intervention to achieve the desired results. In this smart factory, all manufacturing machines and equipment, including all planning and control systems, are interconnected in such a way that they manage, coordinate, and configure themselves throughout the entire process.
THIS smart factory may not be your goal (at the moment) and there are probably good reasons for that. Which brings us to the crux of the matter: This is not to say that you do not (should not) have worthwhile goals when it comes to digitalization.
For small and medium-sized manufacturing companies, digitalization as a goal means using the current capabilities for seamless communication, from sensors to the Internet, to achieve their business goals – and doing so prudently, gradually, and with a clear sense of perspective.
It is about making your factory smarter for YOUR purposes. Your focus is not on technology and its infinite possibilities, but rather on the business goals and constraints of your company.
Digitalization enables you to optimize processes so that you can reduce costs while increasing efficiency, transparency, and quality. It is up to you to decide which processes you want to optimize.
The goal of YOUR digitalization is not to implement an abstract future concept. Your "customized smart factory" tackles the real challenges your company is facing.
One realization is key to this: The biggest shortcoming of digitally assisted manufacturing for SMEs up to now has been overcome — namely, silos and the resulting Babylonian confusion of tongues. It is important to address this issue. After all, a machine pool that is heterogeneous through and through – across different generations, manufacturers, and proprietary developments – can nowadays be connected to a communicating system in plug & play fashion in just a few steps.
The challenge of machine connectivity is no longer a reason not to take sensible digitalization steps or to replace tried-and-tested machinery. It is a recent technological advancement that has benefited SMEs most of all.
By connecting all your machines and equipment on the shop floor via one central interface, your former "soloists" become an orchestra. Your machines now provide uniform data that is complete, meaningfully structured, and prepared in such a way that it can be transmitted via a single interface protocol to your existing or future control, analysis, and visualization tools, and so one.
This is important because by integrating machines in a standardized way, you avoid having parallel systems or complex silos, each mapping only partial aspects of the production process. You also avoid unnecessarily large data volumes (since only the data you require, in the quality you require will ever enter your system). By reducing the volume and complexity of data, you increase both your business and manufacturing-related flexibility.
You are the conductor. In your customized smart factory, you conduct, steer, control, and monitor all the key processes on your shop floor in real time. At the same time, you lay the foundations for connecting your machine data with classic operating data where – and only where – you think it makes sense.
One of the most rewarding goals is to better understand your machines and equipment. Here’s an example: As an experienced foreman, you can usually tell the condition of your machine merely by the sound of it, thanks to your many years of experience. You cannot put a price on that. If you can now also immediately identify the specific problem plaguing the machine, you save yourself the troubleshooting task and get straight to work on eliminating the problem.
The error information necessary for this task is already available in each of your machines. What your machines lack is the ability to "talk" to you, to communicate the cause of the problem to you in a standardized language so that you receive this information. In real time. A connectivity tool offers this very translation service. It makes your machine pool smarter in just a few steps. As smart as you want it to be.