The Smart Factory Glossary | Part 3
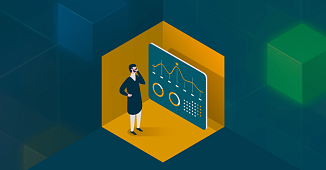
The Smart Factory Glossary | Part 3 – The key acronyms and their definitions
Machine data acquisition, or MDA for short, describes the "interface" between (1) the machine producing the data and (2) the digital collection, storage, and processing of this data. MDA is thus the basic prerequisite for data-driven production, which is referred to as "Industry 4.0" and "Smart Factory".
Effective MDA provides data that creates a whole new level of transparency on the shop floor. This enables (a) the optimization of production control and (b) exposes previously untapped potential for process optimization.
Used wisely, this leads to a sustainable increase in efficiency, flexibility, and quality throughout the entire shop floor. Indeed, it is no coincidence that the use of machine data is deemed to be an essential factor in performance enhancement – thus increasing the competitiveness of any manufacturing company. Let us therefore take a look at the central relationships and terms that shed light on the exciting field of machine data acquisition.
Production volume, capacity utilization, runtime, availability, reliability, machine condition, energy consumption – these are all examples of information that a machine produces or information that can be extracted from a machine or system – in other words, classic machine data.
As a general rule, machine data can be divided into two categories.
Process data:
This includes all information necessary to operate the machine plus all data generated directly as a result of operating the machine. This is primarily control data. However, consumption data, such as power consumption, also counts as process data.
Product data:
This data is measured at the processing units and provides valuable information about the production process. Moreover, data such as the number of pieces, weight, dimensions, temperature, and the distinction between good parts and rejects, etc. is indispensable for ensuring the quality of production.
Regardless of which data you ultimately want to use, step one is always data acquisition. The challenge here lies in connecting your machine(s).
Machine data can be obtained in various ways. For example, sensors that operate independently of the control system can capture specific processes. Alternatively, data is extracted directly from the machine control system and saved to a data logger or made available online for processing.In practice, however, it is apparent that machine data is often still collected manually. This is because automated MDA requires end-to-end networking.
Three distinctions make it easier to understand the challenges of machine networking. This is because the ability to connect to a network varies greatly from one machine to the next.
IP-based networking:
To obtain data automatically, machines and sensors must be fitted with suitable network components. This is because they enable connection to a network, thus allowing data to flow. In industry, IP-based (= Internet Protocol) networking has become widely accepted for this purpose. The medium via which IP communication runs can be an Ethernet cable, Wi-Fi, 5G, etc.
Bus systems:
Networks that are set up with special bus systems pose a challenge for MDA – but not an insurmountable one. While bus systems such as Modbus, EtherCAT, EtherNet/IP, Profinet, Profibus, and CAN are not directly suitable for machine data acquisition, a connectivity solution (see below) can be used to read the required data from the machines.
Connectivity solution:
Modern machines have control systems that are equipped with network connectivity out of the box. These can be quite different (see above) – a stumbling block if they are all to be integrated into ONE network. With older machines and proprietary developments, it is another challenge altogether: in most cases, there is no network connection. In both cases, the solution is a connectivity tool. This hardware/software solution can access the required data at the very point where it is generated: at the corresponding part of the equipment or machine. Regardless of age, manufacturer, proprietary development, etc. In the case of machines with different IP-based networking capabilities, the tool is capable of integrating them despite their differences.The result is a unified layer that connects all the machines on the shop floor (and can also connect all future ones).
The key "takeaway": Concerning the WHEREFROM of the data, there is a solution: EVEN with a heterogeneous machine pool. This is important because the challenges of machine connectivity are often seen as insurmountable (and thus as a major obstacle on the road to Industry 4.0). But that is not the case.
Let us start like this: Every language is based on a set of codes and rules. If you know the codes and rules, you understand the language.
If we translate this to the topic of MDA, this means that every machine speaks its own language. Which one that happens to be, is determined by the communication protocol. In computer science, this term refers to an agreement on how data is transmitted between two or more parties – the aforementioned set of codes and rules.We are now getting to the interesting part: The communication protocols can be standardized – or proprietary (= vendor-specific).
Proprietary protocols:
In the case of a proprietary protocol, the manufacturer has defined its own set of codes and rules. This can have distinct advantages (e.g., the communication speed is usually highly optimized). The problems become apparent, however, the moment the machine is supposed to communicate with other components (with other machines, with an MDA software solution ...). BUT: These are not problems that cannot be overcome. This is because the connectivity tool described above is also the solution here. Either because the "multilingual" connectivity tool translates the protocol into a common language, or because it retrieves the data directly (as described above) and then "translates" it.
Standardized protocols:
These have been defined by associations and consortia to avoid the disadvantages of proprietary protocols. Here, too, a distinction can be made between different "languages". Standards have, in the meantime, become established:
You do not record your machine data just for the sake of it, but because you want to learn from your MDA. In other words, insights and intelligence for decision-making that will help you to safeguard and optimize the performance and quality of your production. To achieve this, you pass on your machine data to a suitable target system, usually an MES software system or an ERP solution.
MES – Manufacturing Execution System:
The title Manufacturing "Execution" System is derived from the short definition of the software solution's function: "A Manufacturing Execution System is used for the continuous control (execution) of existing and valid planning and to provide feedback from the process"*. In other words: An MES enables the digital management, steering, control, and monitoring of production in real time. Just how sophisticated the system is in doing so varies from one solution to the next. Production data (PDA), machine data (MDA), and personnel data are used as data resources, as well as data from other processes that has a real-time impact on the manufacturing/production process.
ERP – Enterprise Resource Planning:
An ERP solution is "higher up" in the enterprise than an MES. This is because the purpose of an ERP system is to map more or less ALL the business processes in an enterprise. The goal of ERP is end-to-end integration and to move away from "silo solutions" in order to manage and optimize the company's resources (capital, personnel, operating resources, materials, information and communication technology) across a network. In addition, ERP systems are designed to make communication flow more smoothly and collaboration within the company more efficient.
So what do both systems have in common? Both MES and ERP as software solutions rely on the availability of data from all machines and equipment (because they do not acquire the data, they "only" process it). And this data needs to be uniform without the "Babylonian confusion of tongues". With the right connectivity solution, this is a prerequisite that can be met. Your machine data acquisition it built on technically solid foundations.
Definition of MES/Manufacturing Execution System, Source: https://en.wikipedia.org/wiki/Manufacturing_Execution_System